|
| |
Caption: Dedication - Locomotive Testing Laboratory (1913) This is a reduced-resolution page image for fast online browsing.
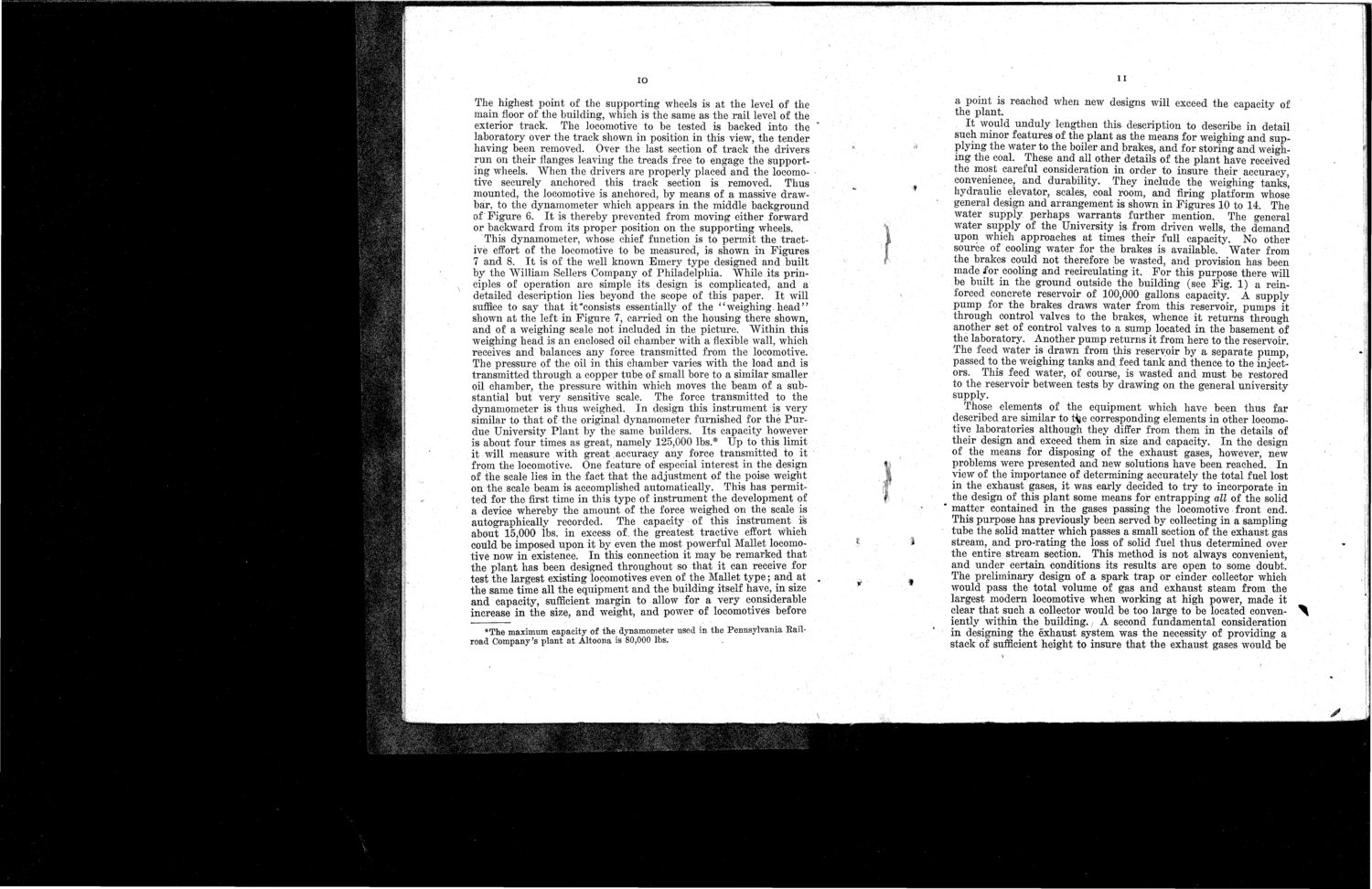
EXTRACTED TEXT FROM PAGE:
10 II The highest point of the supporting wheels is at the level of the main floor of the building, which is the same as the rail level of the exterior track. The locomotive to be tested is backed into the laboratory over the track shown in position in this view, the tender having been removed. Over the last section of track the drivers run on their flanges leaving the treads free to engage the supporting wheels. When the drivers are properly placed and the locomotive securely anchored this track section is removed. Thus mounted, the locomotive is anchored, by means of a massive drawbar, to the dynamometer which appears in the middle background of" Figure 6. It is thereby prevented from moving either forward or backward from its proper position on the supporting wheels. This dynamometer, whose chief function is to permit the tractive effort of the locomotive to be measured, is shown in Figures 7 and 8. It, is of the well known Emery type designed and built by the William Sellers Company of Philadelphia. While its principles of operation are simple its design is complicated, and a detailed description lies beyond the scope of this paper. I t will suffice to say that it "consists essentially of the i i weighing head" shown at the left in Figure 7, carried on the housing there shown, and of a weighing scale not included in the picture. Within this weighing head is an enclosed oil chamber with a flexible wall, which receives and balances any force transmitted from the locomotive. The pressure of the oil in this chamber varies with the load and is transmitted through a copper tube of small bore to a similar smaller oil chamber, the pressure within which moves the beam of a substantial but very sensitive scale. The force transmitted to the dynamometer is thus weighed. In design this instrument is very similar to that of the original dynamometer furnished for the Purdue University Plant by the same builders. Its capacity however is about four times as great, namely 125,000 lbs.* Up to this limit it will measure with great accuracy any force transmitted to it from the locomotive. One feature of especial interest in the design of the scale lies in the fact that the adjustment of the poise weight on the scale beam is accomplished automatically. This has permitted: for the first time in this type of instrument the development of a device whereby the amount of the force weighed on the scale is autographically recorded. The capacity of this instrument is about 15,000 lbs. in excess o l the greatest tractive effort which could be imposed upon it by even the most powerful Mallet locomotive now in existence. In this connection it may be remarked that the plant has been designed throughout so that it can receive for test the largest existing locomotives even of the Mallet type; and at the same time all the equipment and the building itself have, in size and capacity, sufficient margin to allow for a very considerable increase in the size, and weight, and power of locomotives before * The maximum capacity of the dynamometer used in the Pennsylvania Bailroad Company's plant at Altoona is 80,000 lbs. a point is reached when new designs will exceed the capacity of the plant. It would unduly lengthen this description to describe in detail such minor features of the plant as the means for weighing and supplying the water to the boiler and brakes, and for storing and weighing the coal. These and all other details of the plant have received the most careful consideration in order to insure their accuracy, convenience, and durability. They include the weighing tanks, hydraulic elevator, scales, coal room, and firing platform whose general design and arrangement is shown in Figures 10 to 14. The water supply perhaps warrants further mention. The general water supply of the University is from driven wells, the demand upon which approaches at times their full capacity. No other source of cooling water for the brakes is available, "Water from the brakes could not therefore be wasted, and provision has been made for cooling and recirculating it. For this purpose there will be built in the ground outside the building (see Fig. 1) a reinforced concrete reservoir of 100,000 gallons capacity. A supply pump for the brakes draws water from this reservoir, pumps it through control valves to the brakes, whence it returns through another set of control valves to a sump located in the basement of the laboratory. Another pump returns it from here to the reservoir. The feed water is drawn from this reservoir by a separate pump, passed to the weighing tanks and feed tank and thence to the injectors. This feed water, of course, is wasted and must be restored to the reservoir between tests by drawing on the general university supply. Those elements of the equipment which have been thus far described are similar to i%e corresponding elements in other locomotive laboratories although they differ from them in the details of their design and exceed them in size and capacity. In the design of the means for disposing of the exhaust gases, however, new problems were presented and new solutions have been reached. In view of the importance of determining accurately the total fuel lost in the exhaust gases, it was early decided to try to incorporate in ^ the design of this plant some means for entrapping all of the solid # matter contained in the gases passing the locomotive front end. This purpose has previously been served by collecting in a sampling tube the solid matter which passes a small section of the exhaust gas stream, and pro-rating the loss of solid fuel thus determined over the entire stream section. This method is not always convenient, and under certain conditions its results are open to some doubt. The preliminary design of a spark trap or cinder collector which would pass the total volume of gas and exhaust steam from the largest modern locomotive when working at high power, made it clear that such a collector would be too large to be located conveniently within the building./ A second fundamental consideration in designing the exhaust system was the necessity of providing a stack of sufficient height to insure that the exhaust gases would be ^
| |