|
| |
Caption: SWE - Proceedings of the First International Conference of Women Engineers and Scientists This is a reduced-resolution page image for fast online browsing.
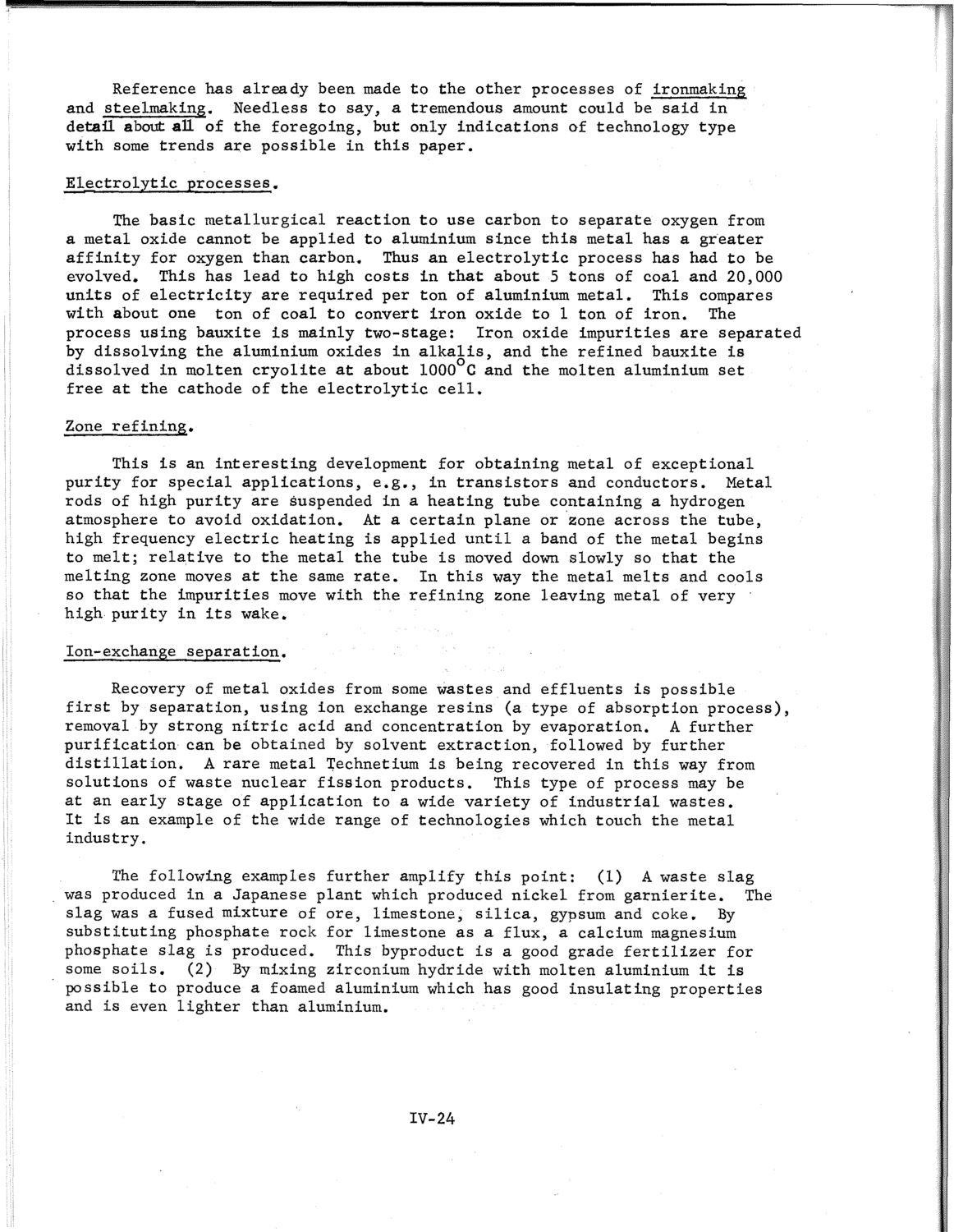
EXTRACTED TEXT FROM PAGE:
Reference has already been made to the other processes of ironmaking and steelmaking. Needless to say, a tremendous amount could be said in detail about all of the foregoing, but only indications of technology type with some trends are possible in this paper. Electrolytic processes. The basic metallurgical reaction to use carbon to separate oxygen from a metal oxide cannot be applied to aluminium since this metal has a greater affinity for oxygen than carbon. Thus an electrolytic process has had to be evolved. This has lead to high costs in that about 5 tons of coal and 20,000 units of electricity are required per ton of aluminium metal. This compares with about one ton of coal to convert iron oxide to 1 ton of iron. The process using bauxite is mainly two-stage: Iron oxide impurities are separated by dissolving the aluminium oxides in alkalis, and the refined bauxite is dissolved in molten cryolite at about 1000 G and the molten aluminium set free at the cathode of the electrolytic cell. Zone refining. This is an interesting development for obtaining metal of exceptional purity for special applications, e.g., in transistors and conductors. Metal rods of high purity are suspended in a heating tube containing a hydrogen atmosphere to avoid oxidation. At a certain plane or zone across the tube, high frequency electric heating is applied until a band of the metal begins to melt; relative to the metal the tube is moved down slowly so that the melting zone moves at the same rate. In this way the metal melts and cools so that the impurities move with the refining zone leaving metal of very high purity in its wake. Ion-exchange separation. Recovery of metal oxides from some wastes and effluents is possible first by separation, using ion exchange resins (a type of absorption process), removal by strong nitric acid and concentration by evaporation. A further purification can be obtained by solvent extraction, followed by further distillation. A rare metal Technetium is being recovered in this way from solutions of waste nuclear fission products. This type of process may be at an early stage of application to a wide variety of industrial wastes. It is an example of the wide range of technologies which touch the metal industry. The following examples further amplify this point: (1) A waste slag was produced in a Japanese plant which produced nickel from garnierite. The slag was a fused mixture of ore, limestone, silica, gypsum and coke. By substituting phosphate rock for limestone as a flux, a calcium magnesium phosphate slag is produced. This byproduct is a good grade fertilizer for some soils. (2) By mixing zirconium hydride with molten aluminium it is possible to produce a foamed aluminium which has good insulating properties and is even lighter than aluminium. IV-24
| |