|
| |
Caption: SWE - Proceedings of the First International Conference of Women Engineers and Scientists This is a reduced-resolution page image for fast online browsing.
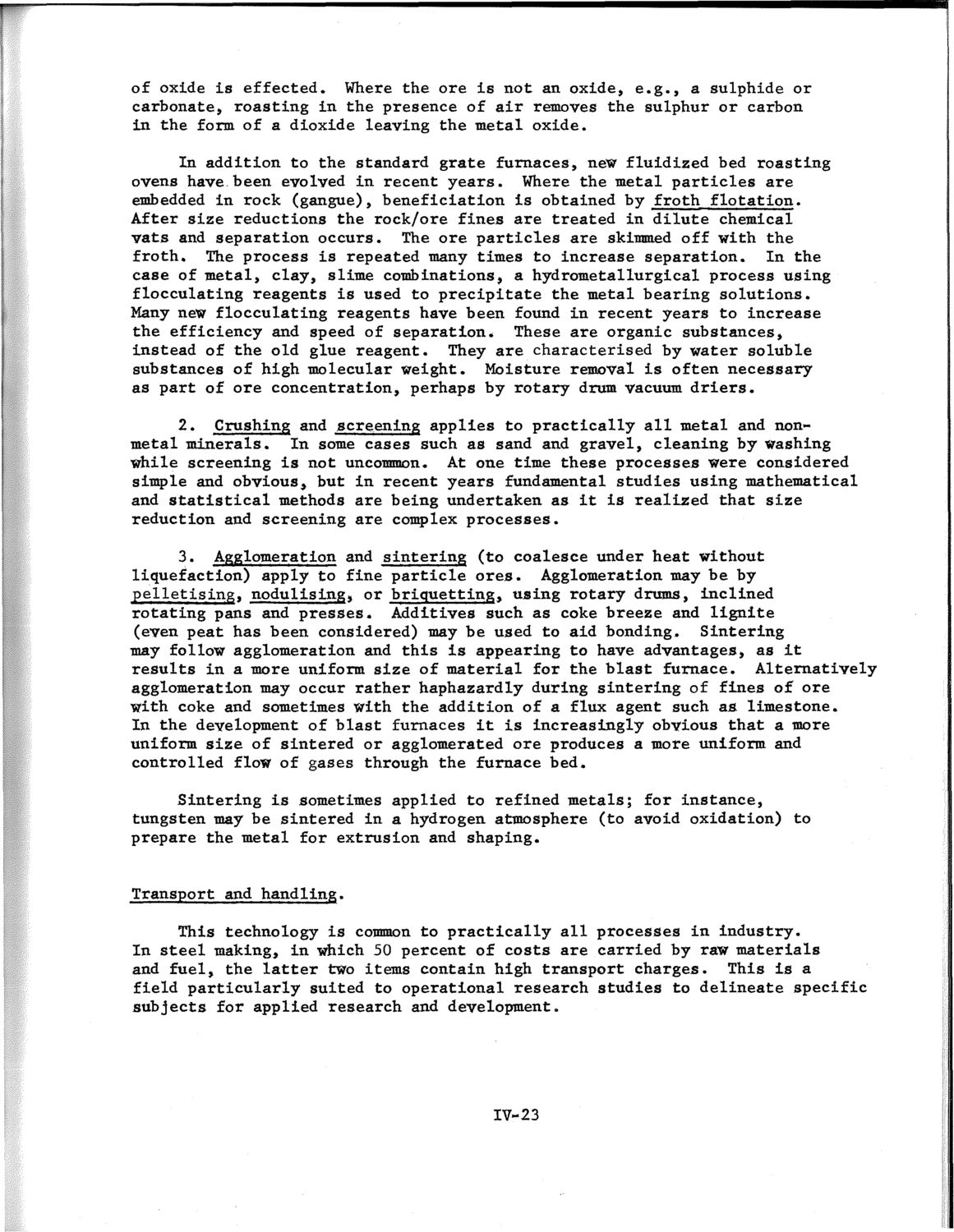
EXTRACTED TEXT FROM PAGE:
of oxide is effected. Where the ore is not an oxide, e.g., a sulphide or carbonate, roasting in the presence of air removes the sulphur or carbon in the form of a dioxide leaving the metal oxide. In addition to the standard grate furnaces, new fluidized bed roasting ovens have been evolved in recent years. Where the metal particles are embedded in rock (gangue), beneficiation is obtained by froth flotation. After size reductions the rock/ore fines are treated in dilute chemical vats and separation occurs. The ore particles are skimmed off with the froth. The process is repeated many times to increase separation. In the case of metal, clay, slime combinations, a hydrometallurgical process using flocculating reagents is used to precipitate the metal bearing solutions. Many new flocculating reagents have been found in recent years to increase the efficiency and speed of separation. These are organic substances, instead of the old glue reagent. They are characterised by water soluble substances of high molecular weight. Moisture removal is often necessary as part of ore concentration, perhaps by rotary drum vacuum driers. 2« Crushing and screening applies to practically all metal and nonmetal minerals. In some cases such as sand and gravel, cleaning by washing while screening is not uncommon. At one time these processes were considered simple and obvious, but in recent years fundamental studies using mathematical and statistical methods are being undertaken as it is realized that size reduction and screening are complex processes. 3. Agglomeration and sintering (to coalesce under heat without liquefaction) apply to fine particle ores. Agglomeration may be by pelletising. nodulising, or briquetting, using rotary drums, inclined rotating pans and presses. Additives such as coke breeze and lignite (even peat has been considered) may be used to aid bonding. Sintering may follow agglomeration and this is appearing to have advantages, as it results in a more uniform size of material for the blast furnace. Alternatively agglomeration may occur rather haphazardly during sintering of fines of ore with coke and sometimes with the addition of a flux agent such as limestone. In the development of blast furnaces it is increasingly obvious that a more uniform size of sintered or agglomerated ore produces a more uniform and controlled flow of gases through the furnace bed. Sintering is sometimes applied to refined metals; for instance, tungsten may be sintered in a hydrogen atmosphere (to avoid oxidation) to prepare the metal for extrusion and shaping. Transport and handling. This technology is common to practically all processes in industry. In steel making, in which 50 percent of costs are carried by raw materials and fuel, the latter two items contain high transport charges. This is a field particularly suited to operational research studies to delineate specific subjects for applied research and development. IV-23
| |