|
| |
Caption: SWE - Proceedings of the First International Conference of Women Engineers and Scientists This is a reduced-resolution page image for fast online browsing.
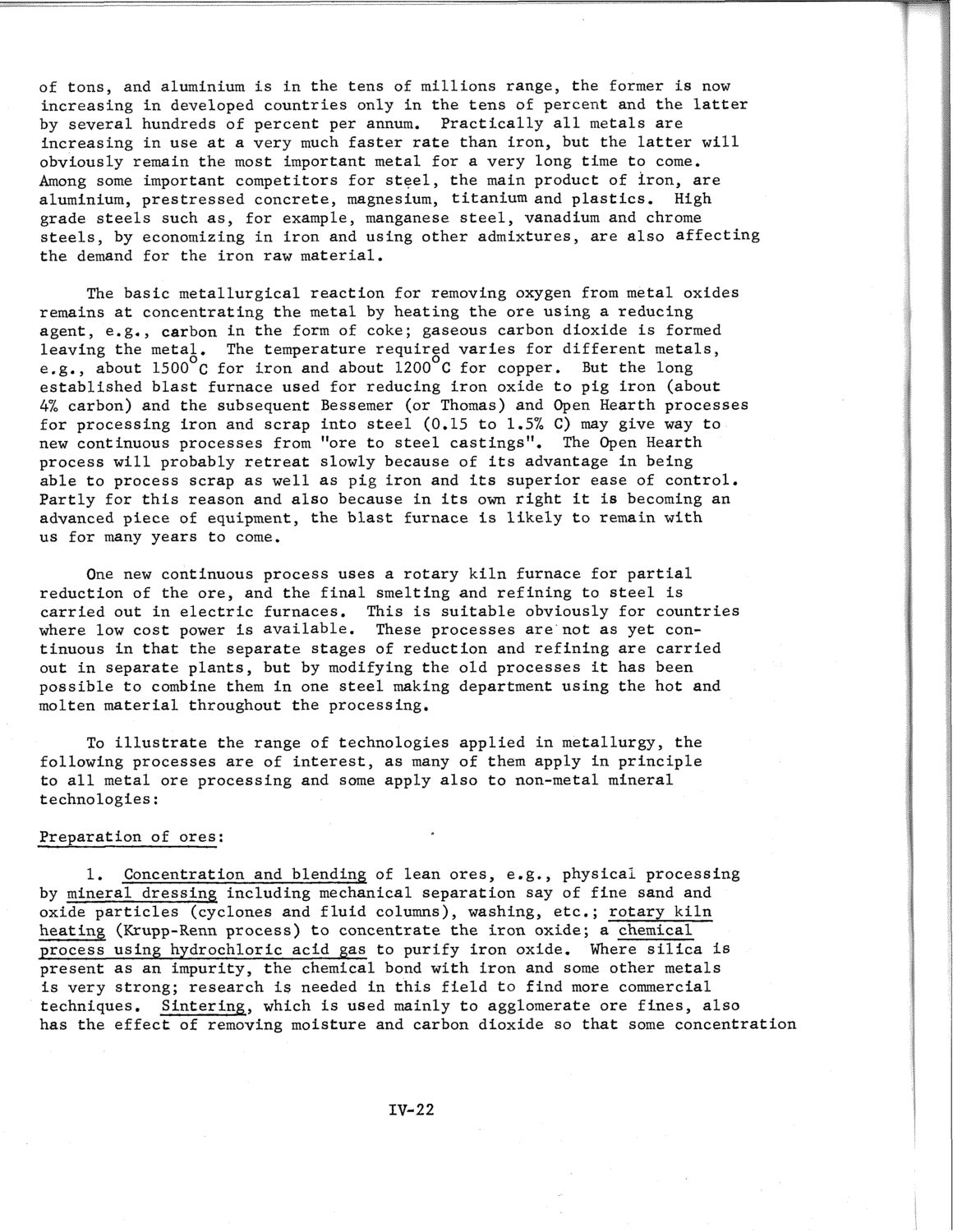
EXTRACTED TEXT FROM PAGE:
of tons, and aluminium is in the tens of millions range, the former is now increasing in developed countries only in the tens of percent and the latter by several hundreds of percent per annum. Practically all metals are increasing in use at a very much faster rate than iron, but the latter will obviously remain the most important metal for a very long time to come. Among some important competitors for steel, the main product of iron, are aluminium, prestressed concrete, magnesium, titanium and plastics. High grade steels such as, for example, manganese steel, vanadium and chrome steels, by economizing in iron and using other admixtures, are also affecting the demand for the iron raw material. The basic metallurgical reaction for removing oxygen from metal oxides remains at concentrating the metal by heating the ore using a reducing agent, e.g., carbon in the form of coke; gaseous carbon dioxide is formed leaving the metal. The temperature required varies for different metals, e.g., about 1500 C for iron and about 1200 C for copper. But the long established blast furnace used for reducing iron oxide to pig iron (about 4% carbon) and the subsequent Bessemer (or Thomas) and Open Hearth processes for processing iron and scrap into steel (0.15 to 1.5% C) may give way to new continuous processes from "ore to steel castings". The Open Hearth process will probably retreat slowly because of its advantage in being able to process scrap as well as pig iron and its superior ease of control. Partly for this reason and also because in its own right it is becoming an advanced piece of equipment, the blast furnace is likely to remain with us for many years to come. One new continuous process uses a rotary kiln furnace for partial reduction of the ore, and the final smelting and refining to steel is carried out in electric furnaces. This is suitable obviously for countries where low cost power is available. These processes are not as yet continuous in that the separate stages of reduction and refining are carried out in separate plants, but by modifying the old processes it has been possible to combine them in one steel making department using the hot and molten material throughout the processing. To illustrate the range of technologies applied in metallurgy, the following processes are of interest, as many of them apply in principle to all metal ore processing and some apply also to non-metal mineral technologies: Preparation of ores: 1. Concentration and blending of lean ores, e.g., physical processing by mineral dressing including mechanical separation say of fine sand and oxide particles (cyclones and fluid columns), washing, etc.; rotary kiln heating (Krupp-Renn process) to concentrate the iron oxide; a chemical process using hydrochloric acid gas to purify iron oxide. Where silica is present as an impurity, the chemical bond with iron and some other metals is very strong; research is needed in this field to find more commercial techniques. Sintering, which is used mainly to agglomerate ore fines, also has the effect of removing moisture and carbon dioxide so that some concentration IV-2 2
| |